Carbon fiber is always considered better than steel because of its higher stress-resistant properties and lighter weight. It is more expensive to manufacture, but in a mass production environment, prices come down. So it only makes sense that, at some point, carbon fiber will eventually find its way into many products that we normally associate as only possible with steel. Like engine blocks, that’s why Nissan just patented its carbon fiber engine.
Is the entire block made of carbon fiber?
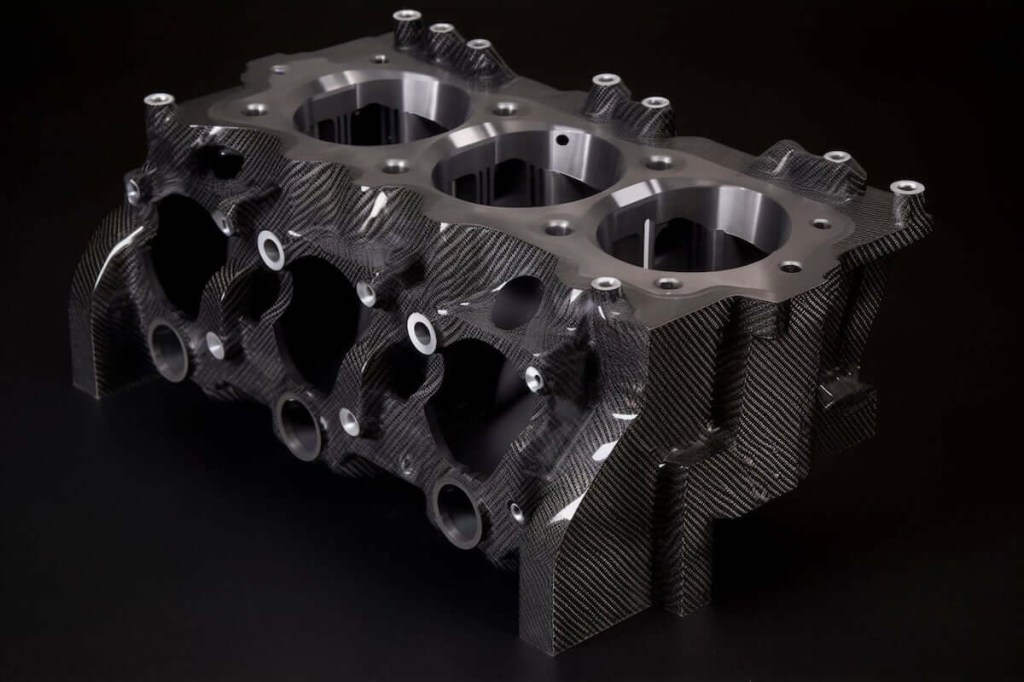
It’s not all carbon fiber. There are still steel cylinder liners, with the carbon fiber acting to hold them in place, so to speak. But it makes us wonder if an entire blog could one day be entirely of the material.
As Nissan imagines this first stab at carbon fiber used for an engine is with a main block, which are the cylinders themselves. Carbuzz says the patent describes “A resin outer member that is welded to the main block.” There are gaps between the main block and the outer carbon fiber, which become water passages. It also helps insulate the outer material from the heat generated in the cylinders.
This has always been the downside of considering carbon fiber as an engine block material. The resins used in the manufacture of carbon fiber can only withstand temperatures of about 250 degrees. Most engines never reach this temperature.
What are some of the disadvantages of a carbon fiber engine?

But thermal temperatures differ throughout an engine block. Carbon fiber mat can take a lot of heat, but not resin. This is especially true with the friction of the piston on the cylinder walls. That’s why Nissan has chosen metal cladding.
And another problem with carbon fiber as an engine block material is that oil, antifreeze and fuel could attack the resin. Especially oil can be a very aggressive chemical. Any of these could cause the mat to delaminate.
Iron is not the only material for engine blocks. Aluminum, magnesium and even titanium engine blocks have seen the light of day. Of course, aluminum engine blocks have been around for years.
Magnesium is also a light replacement for iron. But magnesium alloys don’t have the same strength as good old iron. But there are magnesium engines in production. Porsche used magnesium blocks from 1968 to 1977. But then so did Ford, Mercedes-Benz, Jaguar and even Kia.
Wouldn’t titanium be a better engine block?
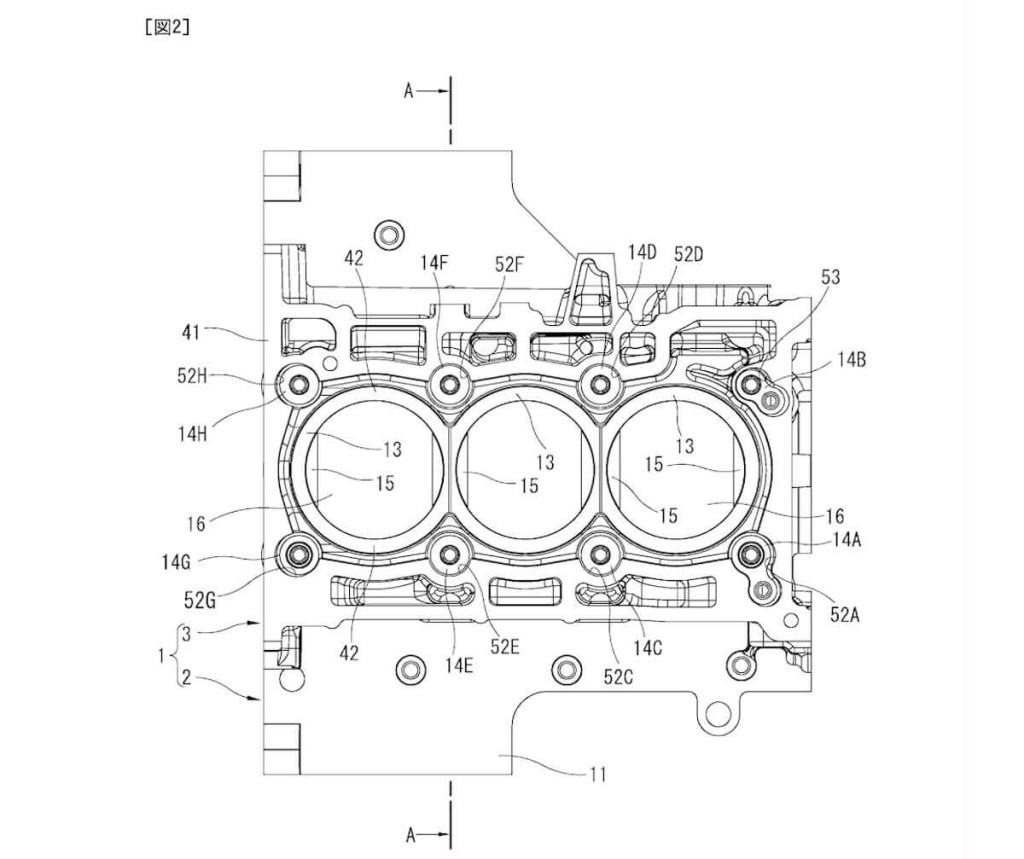
As for titanium, yes, it would be a great substitute for iron, except for a few things. First, it is extremely expensive, so it almost kills mass production. But it is also difficult to machine. Because there are different varieties and alloys for titanium, they pose different difficulties during machining. And exposing the solder to oxygen or nitrogen can cause severe embrittlement.
Nissan is well aware of the issues involved in creating a carbon fiber engine block, as we can see. One of the advantages you’re looking for is that operating temperatures rise faster than with iron or aluminum. This should reduce the possibility of premature wear on certain surfaces.
But until further developments, both carbon fiber and titanium are found in a multitude of engine components such as valves, piston rods and fasteners.